GOLDROCKMINER® HARD ROCK MINING EQUIPMENT, GOLD MINING EQUIPMENT, GOLD MINING ROCK CRUSHER
DOVE is the world’s major manufacturer of an unmatched range of Semi-stationary Hard Rock mining equipment and crushing plants, for gold, platinum metals, base metals, and ferrous metals, producing high quality Ball Mills, Jaw Crushers, Cone Crushers, Magnetic Separators, Shaking Tables, Gold Concentrators, Rotary Dryers and Flotation Process.
GOLDROCKMINER® Plants are designed exclusively by DOVE and are combination of hard rock crushing and processing plant. Each plant is customized and designed based on mineral composition of the ore and specification of each mining site. DOVE mineral laboratory provides detailed mineral analysis of your ore samples.
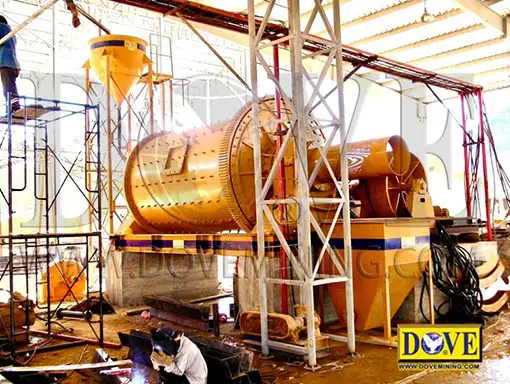
GOLDROCKMINER® Ball Mills.
FEATURES:
- EFFICIENCY: GOLDROCKMINER® Plants are configured with DOVE advanced technology, for 100% recovery of gold and other metals production.
- ENVIRONMENT-FRIENDLY: GOLDROCKMINER® Plants are 100% environment-friendly, use no chemicals (no mercury, no cyanide), use only recycled water.
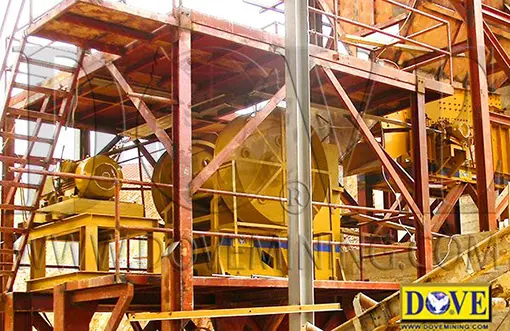
GOLDROCKMINER® Jaw Crusher.
- USER-FRIENDLY: GOLDROCKMINER® Hard Rock Plants only require 2-3 days of training to learn the operation and maintenance, with little prior experience.
- RUGGED DESIGN: GOLDROCKMINER® Hard Rock Plants offer durability and the longevity of operations on the mining sites, as they are built with the highest quality of material and workmanship.
- ECONOMICAL: GOLDROCKMINER® Hard Rock Plants are highly efficient and economical and require very little maintenance, and minimum operator interference.
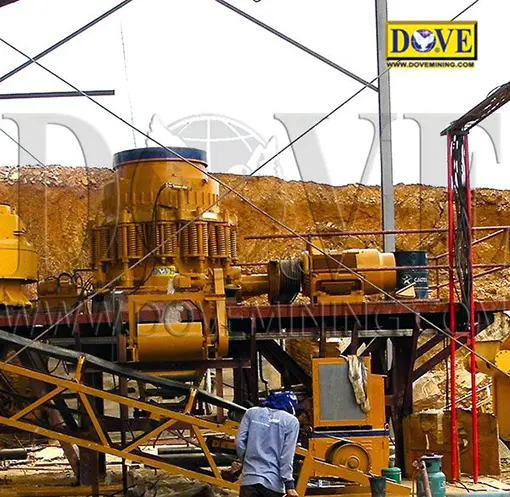
GOLDROCKMINER® Cone Crusher.
DOVE GOLDROCKMINER® Gold Mine, Laos.
DOVE GOLDROCKMINER® Gold Mine, Sudan.
WIDE RANGE:
DOVE is the leader and powerhouse in the mining equipment manufacturing industry and over the last 50 years has produced the largest range of Semi-stationary Hard Rock Plants (GOLDROCKMINER® Hard Rock Processing Plants) for small, medium and large-scale hard rock mining operations, with the capacity to handle material ranging from 2-2,000 TPH solids.
Semi-stationary hard rock processing plants, also known as Semi-stationary Crushing Plants, Crushing and Grinding Plants are processing plants designed for the efficient processing of the valuable minerals contained in a Hard Rock (Primary) deposit, for the recovery of Gold, Platinum metals, Base metals, Ferrous metals and Light metals.
DOVE Semi-stationary Hard Rock Plants are the most advanced processing plants in the mining industry, with unique features and designs, and the highest recovery rate. DOVE Semi-stationary hard rock processing plants are economical, with the highest and fastest return on investment.
Please, visit our PROJECT GALLERY
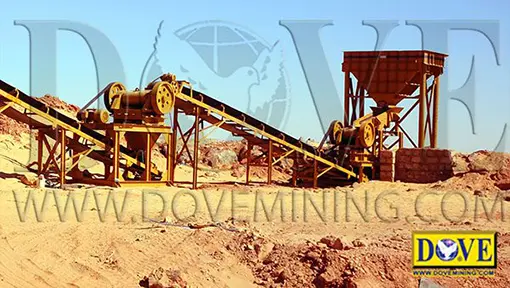
GOLDROCKMINER® Feed Hopper, Vibrating Grizzly, Jaw Crushers and Belt Conveyors.
DOVE Hard Rock Plants and recovery methods vary depending on several factors, including the size of the rock, the rock’s condition, the hardness of the materials, minerals composition in the ore, specific gravity and other characteristics and specification of the elements to insure the efficient recovery of 100% of the minerals Production, with no loss.
Hard rock mining is the process of extracting metals and minerals encased in rocks (primary deposit). Hard rock ore can contain metals, minerals such as gold, platinum, silver, iron, copper, manganese, zinc, nickel, tin and lead, zircon, etc.
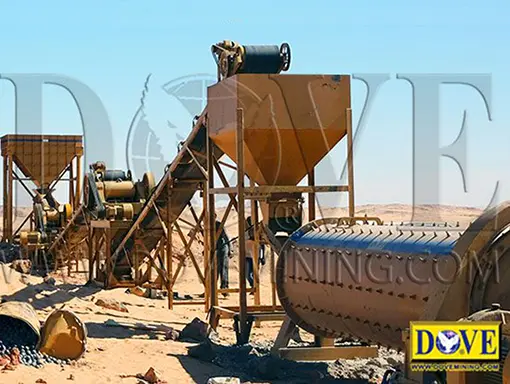
DOVE Hard Rock Gold Mining Equipment.
WARRANTY:
All DOVE equipment carry a standard Manufacturer’s Warranty, which can be extended to 5 years, in addition to lifetime spare parts supply service.
DOVE provides full technical services worldwide, including plant engineering design, mining site construction design, site assembly, installation, test run and training.
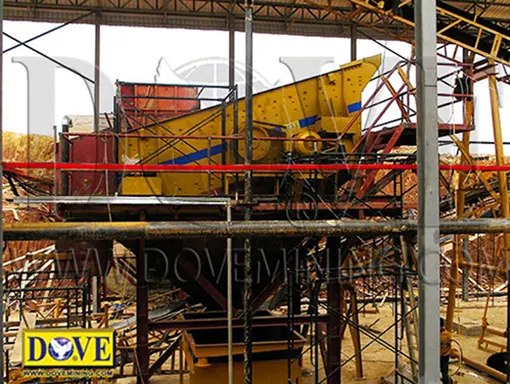
GOLDROCKMINER® Vibrating Screen.
MANUFACTURING FACILITIES:
DOVE Equipment & Machinery manufacturing facilities are located about 30 minutes drive from the company Head office in Bangkok, which includes 8 factories and showroom.
DOVE Equipment and Machinery with over 50 years manufacturing expertise, and the largest range of mining and minerals processing technologies is the recipient of ISO 9001: 2015, Green Industry Certification, and Golden Eagle of Asia Awards 2020 Best Business of the Year (DOVE Equipment and Machinery and DOVE Instruments), which insures highest quality and standard of our manufacturing and customer service practices.
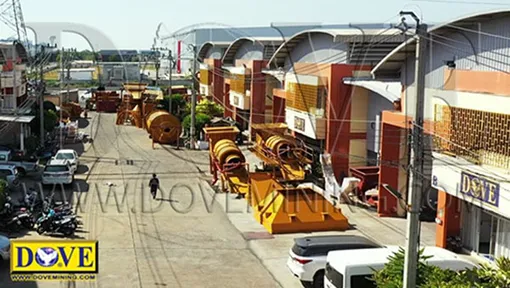
DOVE Manufacturing Facilities.
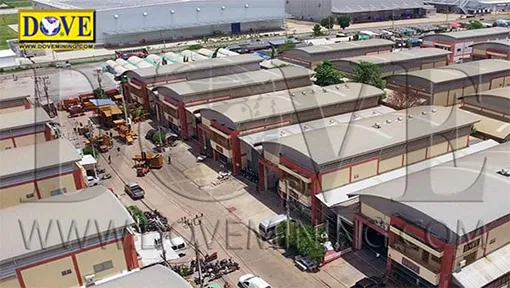
DOVE Equipment and Machinery 8 Factories.
Video of DOVE Manufacturing Facilities:
MINERAL TEST SERVICES:
DOVE laboratory will assay your ore samples rapidly and analyze your raw materials and recommend the most efficient processing plant according to the ore specifications, minerals composition, and ore assay results, and your project size and the geologic and topographic conditions of your mine.
Please, CONTACT US for your sample analysis and quotation.
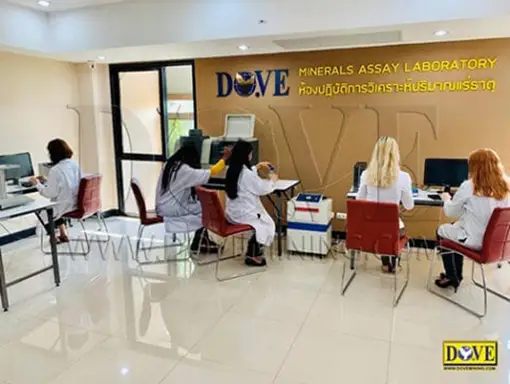
DOVE SEMI-STATIONARY HARD ROCK PLANTS CONFIGURATION
DOVE Semi-stationary Hard Rock Plants unique designs are embedded in every single one of their components to insure efficient operations and 100% recovery of the Gold, Tin, Iron, Tantalite, Manganese and other metals and minerals production, with no loss.
Ore feeding, Crushing (Coarse and Fine), Grinding (or milling), Sizing (screening and classification) and Concentration (separation and recovery) are the three most important steps that are involved in ore processing by Hard Rock Plants. Overlooking any short of these steps will result in lack or reduction of recovery, as well as the loss of the valuable minerals.
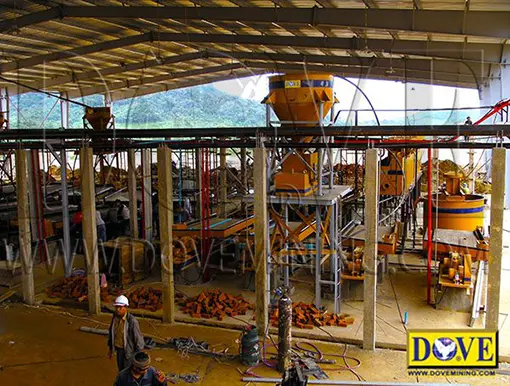
GOLDROCKMINER® Hard Rock Plant
In a hard rock plant, the concentration (recovery and separation) stage is achieved by a method scientifically called “Gravity Separation”. The separation occurs when the metals and mineral are subjected to a variety of forces in a medium (e.g. water, air, other heavy medium) to trigger a response, which is usually enhanced resistance or accelerated settling time of said metals and minerals, depending on their specific gravity.
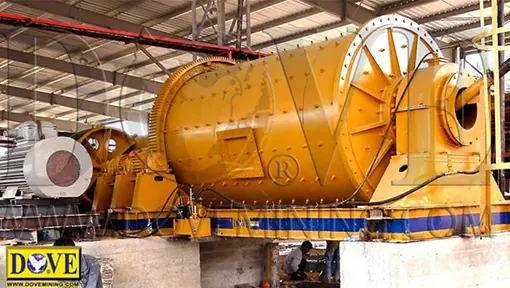
Ball Mill.
The major components of DOVE Semi-stationary Hard Rock Plants are as below:
STEP 1: ORE FEED
1.1 ORE FEED HOPER:
consists of a large hopper designed to feed the ore to the rest of the hard rock plant. The hopper, in a hard rock process, usually allows for dry feed of the rocks to the plant. It is designed for a direct feed by earth moving equipment. The size of the feed will depend on the plant’s capacity (TPH).
DOVE Ore Feed Hoppers are supplied in wide range of capacities, and are designed and engineered as parts that fit to make the hopper. This feature allows the hopper to easily be shipped in standard containers and rapidly be assembled and installed once on site.
DOVE Ore Feed Hoppers are built with thick and heavy sides that provides strength and endurance to the severe conditions of the mining site.
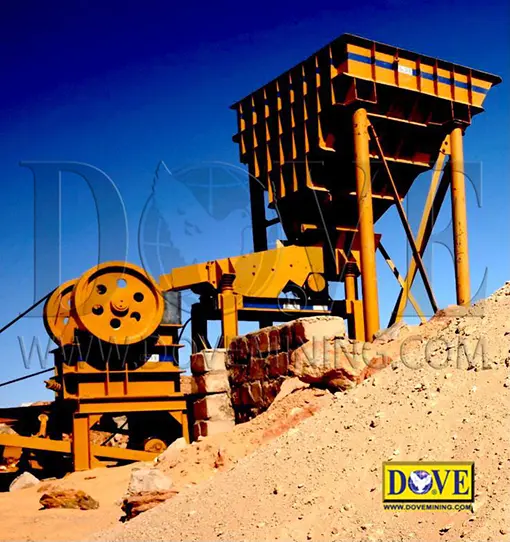
Feed Hopper, Vibrating Grizzly, Jaw Crusher.
1.2 VIBRATING or GRIZZLY FEEDER:
it is a device set between the hopper and belt conveyor, or any equipment fed by the hopper. This device will ensure that the material coming from the feed hopper is efficiently and smoothly fed to the next equipment. The vibrating feeder prevents the hopper from being clogged by the accumulation of rocks and allows the next equipment to be safely fed without having to endure the stress of rocks falling directly on it, which could accelerate wear and tear, and result in damage.
DOVE Feeders are a wide variety of vibrating feeders that can be configured with grizzly bars to screen the oversized rocks contained in the ore to ensure efficient processing and recovery of the minerals in the next stages, and to protect the next equipment from the potential damages that could occur from an impact with said rock. The screening sizes vary depending on the ore characteristics and project specifications.
Because of their strong build, DOVE Feeders have a proven history of optimal efficiency and durability, even when handling large rocks.
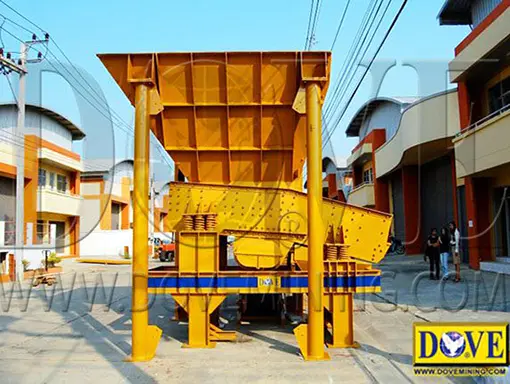
Hopper and Vibarting Grizzly Feeder.
1.3 BELT CONVEYOR:
works as the means by which the ore, rocks or dry sand in a solid form, is efficiently transported throughout the processing plant. DOVE Belt Conveyors are in various dimensions to cater to the ore logistics capacity requirements of the processing plant as well as the mining site characteristics.
DOVE Conveyors’ belts are built with high quality thick rubber that can withstand the weight of material with minimum. DOVE Belt Conveyors are supplied with high resistance support stand, with reinforced structure.
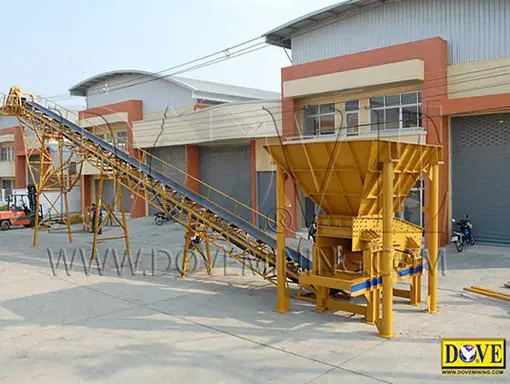
Feed Hopper and Belt Conveyor.
STEP 2: CRUSHING (COARSE AND FINE)
2.1 JAW CRUSHER
is a device designed to reduce the size of a rock. It breaks the particles by applying a compressive force to them. The two jaws applying a mechanical pressure to the particles achieve this. A jaw crusher consists of a set of vertical jaws, one of which is stationary, while the other jaw called swings back and forth, relatively to the stationary jaw. The crusher acts like a nutcracker on the particles.
DOVE Jaw Crushers come in various designs and capacities, aimed to handle all stages of crushing, from primary to tertiary, of various types of rocks such as granite, quartz, gravel, and many more. DOVE Jaw Crushers are configured with optimum cavities. Their height is designed in relation to the feed opening to ensure minimum clogging of the material, resulting in higher crushing efficiency, all in a compact design.
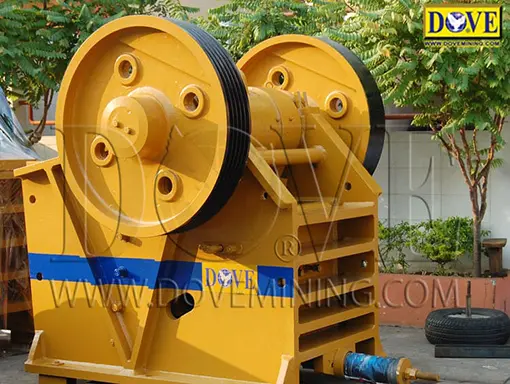
Jaw Crusher.
2.2 CONE CRUSHER
is a device designed to reduce rocks into smaller rocks or dust. It operates using a mantle that rotates within a bowl. The material is compressed between an eccentrically rotating piece of steel, called the mantle, and a stationary piece of steel, called the bowl. The material works its way down along the crushing chamber, as it gets smaller, until the crushed material is discharged at the bottom of the machine.
DOVE Cone Crushers are designed to handle various capacities and material hardness, in secondary and tertiary crushing operations, for limestone, granite, basalt, quartzite, river gravel, and many more. DOVE Cone Crushers are designed for rapid Field Adjustment and Continuous Lubrication. They are configured with Hydraulic Cleaning units and Hydraulic Lifting Arm.
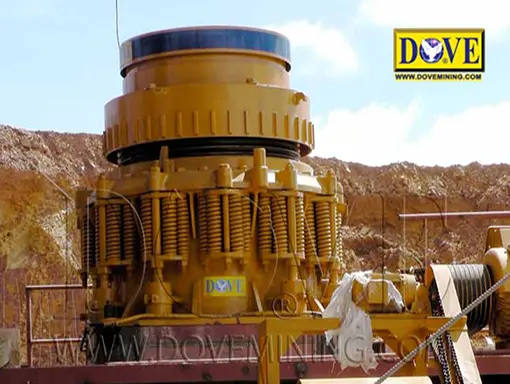
Cone Crusher.
2.3 IMPACT CRUSHER
is a device that breaks up material by either striking it with a bowl bar that moves rapidly, or by throwing the material into a stationary anvil where it will break upon impact. They are utilized in aggregates operation, mining operations and recycling operations.
DOVE Impact Crushers are designed and supplied in various models, and are used for hard material crushing operation. The material can be bauxite, coal, coke, magnetite, mica, salt, slate, and many more. DOVE Impact Crushers’ rolls are made of various alloys, from manganese or Tacm, and can be easily adjusted by increasing or decreasing the shims.
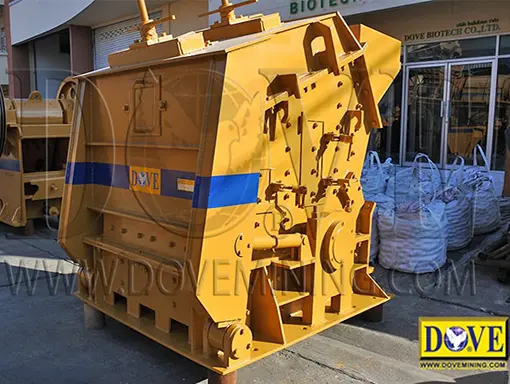
Impact Crusher.
STEP 3: GRINDING
3.1 BALL MILLS
are devices, used in mineral dressing processes and other operations (paints, pyrotechnics, ceramics, and selective laser sintering, for the grinding of materials. This device is used in DOVE Semi-Stationary Hard Rock plants to grind the ore until the liberation size of valuable minerals is reached. The size reduction is achieved by impact and attrition. When the shell rotates, the balls are dragged to almost the top of the shell, and from there, they fall unto the material, which breaks due to impact, DOVE Ball Mills are deigned for either wet or dry grinding of materials, in various models, to cater to the liberation size of the minerals and the hardness of the ore. DOVE Ball Mills can be used in various industries such as mining, construction and aggregate, chemical, pyrotechnics, ceramics, waste processing, food processing, and many more.
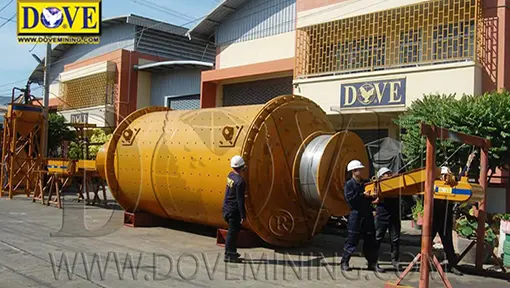
DOVE Ball Mill.
STEP 4: SREENING (SIZING AND CLASSIFICATION)
4.1 VIBRATING SCREENS
are used in DOVE Hard Rock Processing Plants to classify the different ranges of particles contained in the ore and ensure that the right sizes of materials goes to the right processing stages, ensuring a high efficiency delivered during said processing stages. The screen sizes depend on the ore characteristics, project specifications and on the plant configuration.
DOVE Vibrating Screens can be configured with multiple decks to efficiently and simultaneously separate various sizes of material from one another. DOVE offers a wide range of Vibrating Screens, with different mesh sizes, number of decks and various capacities. The parameters of the DOVE Vibrating Screens are customized to cater to each mining project, individually.
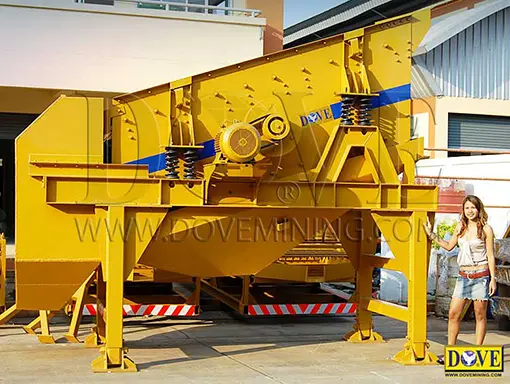
DOVE Vibrating Screen.
STEP 5: CONCENTRATION (COARSE AND FINE)
5.1 CENTRIFUGAL CONCENTRATORS
are a type of gravity concentration apparatus, predominantly used in the gold mining industry. It is used for the recovery of fine particles of free gold, meaning gold that does not require gold cyanidation for recovery.
Gold centrifugal concentrators have been developed over the past century and allow for mining operations to trap a higher percentage of the fine gold and other precious metals in black sands that used to be lost into the tailing ponds. Centrifugal gold concentrators operate using G-forces, which allow for separation of the heavier particulate including fine gold and other metals.
DOVE Centrifugal Concentrators are configured for automatic and continuous recovery, using only recycled water to process and to recover 100%, down to 40 microns (0.004 mm), of all fine the gold, silver, platinum group metals, and other precious metals contained in the processed ore.
DOVE Gold Concentrators are integrated with a complete hydraulic system, as well as feed and moisture adjustment mechanism, to eliminate freezing conditions and regulate the flow of the material.
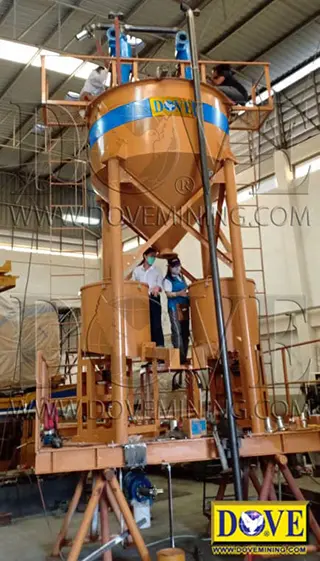
DOVE Centrifugal Concentrator.
5.2 CONCENTRATING TABLE (SHAKER TABLE)
can be considered a thin film, shear flow process equipment that separates particles of the material being fed to it based on the differences in their specific gravity, density, size and shape. Mineral rich particles, from light to heavy and fine to coarse will be effectively sorted by net effective weight on the Concentrating Table.
Concentrating Tables have been used are recognized as the most effective and selective machines for wet gravity separation, and have been proving their efficiency in producing a high-grade concentrate, while handling a wide range of specific gravities, for many years. They are mostly used for the final cleaning stages to produce final concentrates.
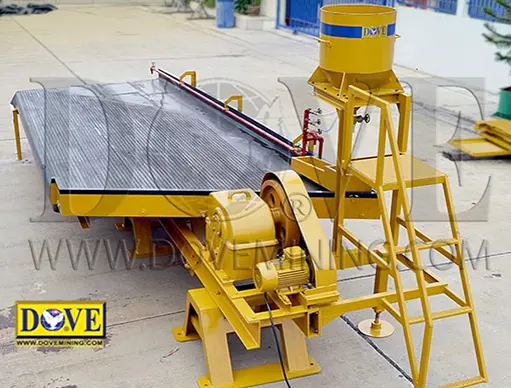
DOVE Shaker Table.
DOVE Concentrating Tables are designed with rectangular or diagonal wooden or aluminum decks, covered with one-piece of ultra-smooth rubber riffle surface. The riffle pattern can be sand riffling, slime riffling, or individual riffle patterns, depending on the individual separation requirements.
DOVE Concentrating Tables are extremely selective wet gravity separation devices that offer exceptional efficiency in material separation that other existing tables in the industry, with rough-surface covering, cannot achieve.
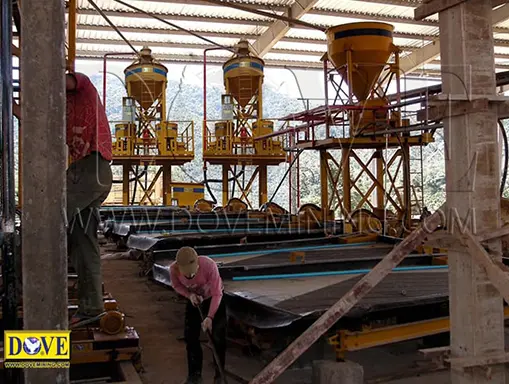
DOVE Concentrating Tables and Centrifugal Concentrators at the mining site.
WE HIGHLY RECOMMEND FORWARDING SOIL SAMPLES OF YOUR MINE TO US FOR ANALYSIS, IN ORDER TO DESIGN AND RECOMMEND THE MOST EFFICIENT PROCESSING PLANT, TAILOR MAID TO YOUR MINE REQUIREMENTS, FOR HIGHEST PRODUCTION RECOVERY.