GOLD MINING EQUIPMENT, DIAMOND MINING EQUIPMENT, GOLD WASH PLANTS, GOLD TROMMEL, SHAKER TABLE, GOLD DREDGE, BALL MILL, JAW CRUSHER, MAGNETIC SEPARATOR, GOLD PROSPECTING EQUIPMENT
GOLD MINING EQUIPMENT, DIAMOND MINING EQUIPMENT, GOLD WASH PLANTS, GOLD TROMMEL, SHAKER TABLE, GOLD DREDGE, BALL MILL, JAW CRUSHER, MAGNETIC SEPARATOR, GOLD PROSPECTING EQUIPMENT
DOVE IS A LEADING MANUFACTURER OF ALLUVIAL & HARD ROCK GOLD MINING EQUIPMENT, DIAMOND MINING EQUIPMENT, AND THE LARGEST RANGE OF MINERALS PROCESSING PLANTS FOR BASE METALS, FERROUS METALS AND OTHER MINERALS.
COMPLETE MERCURY-FREE, CYANIDE-FREE SOLUTIONS — ENGINEERED FOR THE HIGHEST RECOVERY OF GOLD, DIAMONDS, AND OTHER MINERALS.
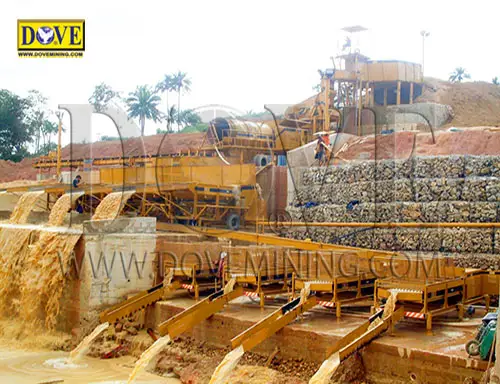
DOVE MEGAMINER® Alluvial Processing Plant.
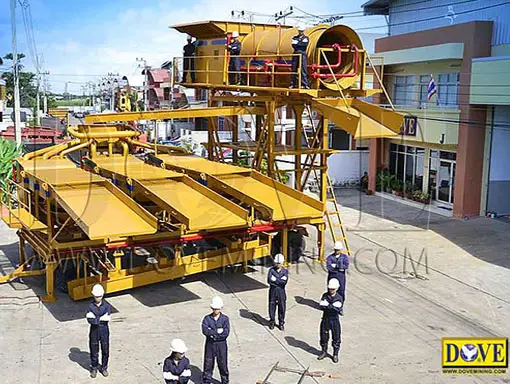
SUPERMINER® Mobile Alluvial Processing Plant.
ALLUVIAL MINING EQUIPMENT / WASH PLANTS
DOVE is the largest manufacturer of the full range of alluvial Gold Mining Equipment, Gold wash plants, Diamond mining equipment, and processing plants for Base Metals, Ferrous Metals, Light Metals.
- EXPLORER® Portable Plants, 47 models, with capacity ranging from 3-1,000 TPH (solids).
- SUPERMINER® Mobile Processing Plants, total 46 models, capacity range of 10-200 TPH (solids).
- MEGAMINER® Stationary and Semi-Stationary processing plants, capacity range of 10-6,000 TPH (solids).
DOVE Gold Mining Equipment and Diamond wash plants are designed for 100% recovery of Gold and Diamond production, with no loss.
DOVE gold wash plants and diamond wash plants are configured with production security system and locking mechanism to prevent the theft of production.
DOVE Diamonds and Gold mining equipment is configured for different ore type, laterite, heavy clay, gravel and black sand. Wash plants are designed for highest recovery and minimum operator requirements.
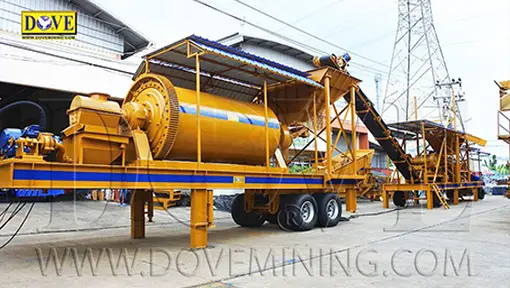
SPEEDMINER® Mobile Hard Rock Gold Plant.
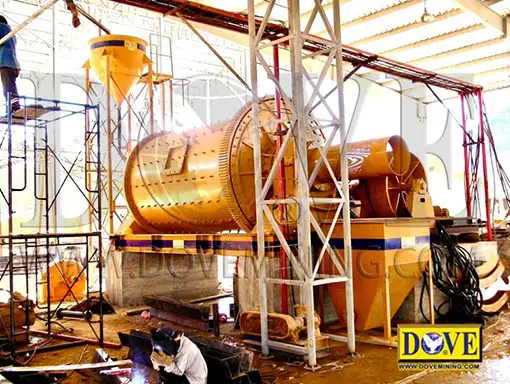
GOLDROCKMINER® Hard Rock Gold Plant.
HARD ROCK MINING EQUIPMENT, CRUSING PLANTS, GOLD MINING EQUIPMENT
DOVE is a major manufacturer of hard rock gold mining equipment, and hard rock mining equipment, and crushing plants for base metals, ferrous metals and light metals, producing Ball Mills, Jaw Crushers, Cone Crushers, Magnetic Separators, Shaking Tables, Gold Concentrators, Rotary Dryers, and Flotation Process.
- SPEEDMINER® Mobile Hard Rock Plants, produced in 13 models with the capacity range of 2-120 TPH (solids).
- GOLDROCKMINER® Semi-stationary Hard Rock Processing Plants with capacity range of 2-2,000 TPH (solids).
Each processing plant is designed tailor made according to the ore characteristics and the mineral composition of the ore, and designed for the 100% recovery of gold and other metals production, with no loss.
DOVE Hard Rock Plants are built with the highest quality of material to ensure durability of all components.
DOVE MINERAL LABORATORY CAN ANALYSE YOUR ORE SAMPLES
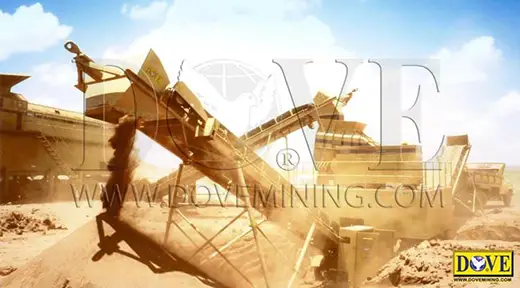
DESERTMINER® Dry Processing Plant.
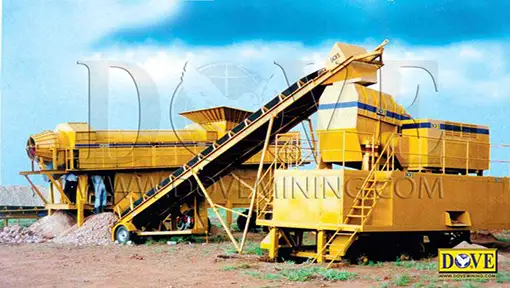
DESERTMINER® Dry Processing Plant.
DRY GOLD MINING EQUIPMENT, DRY PROCESSING PLANTS
DESERTMINER® is a Dry Mineral Processing Plant developed by DOVE to simultaneously concentrate, separate and recover gold, platinum group metal, base metals, ferrous metals from Alluvial deposits, as well as Hard Rock deposits, which are located in dry areas, where water not available.
DESERTMINER® is designed and configured to deliver a high efficiency in mineral processing, with 100% recovery of gold and other metals and minerals, with no loss, similarly to the wet mineral processing plants.
DESERTMINER® plants are produced in wide range of models, both for Alluvial and Hard Rock deposits, as below:
- DESERTMINER® – configured for dry processing of placer (alluvial applications), produced in 8 models, with the capacity range of 2-50 TPH.
- DESERTMINER® – configured for dry processing of primary (hard rock applications), produced in 8 models, with the capacity range 2-50 TPH.
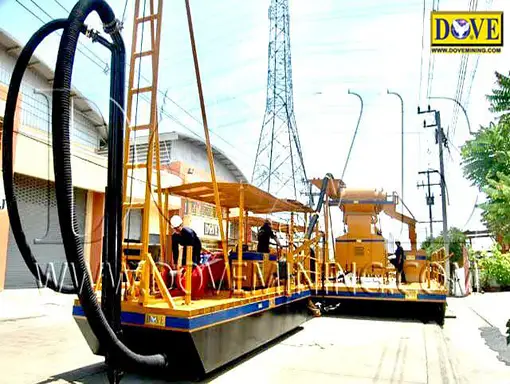
DOVE Dredging equipment
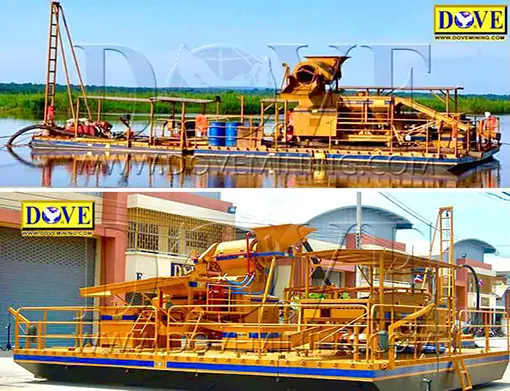
DOVE RIVERMINER®: Dredge and Floating Plant
DREDGING EQUIPMENT, GOLD DREDGING EQUIPMENT, FLOATING PLANTS
DOVE is the world major manufacturer of dredging equipment, gold dredging equipment and Floating Plants for river mining of gold, diamonds, gemstones, tin, etc.
- Gold dredges, diamond dredges, produced in various configurations: suction dredge plants (10 models, with capacity range 80-2,800 m3/Hour) slurry. Cutter suction dredge plants (6 models, with capacity range 800-2,800 m3/Hour) slurry.
- Floating plants to process gold, diamond and gemstones without transporting material on shore, produced in 18 models, with capacity range of (80-1,000 m3/Hour) slurry.
- Complete integrated processing lines for river mining – RIVERMINER® is a combination of DOVE powerful Dredge and Floating Plant, produced in 18 models with capacity range of (80-1,000 m3/Hour) slurry.
DOVE dredges do not require divers.
DOVE dredging equipment and Floating Plants provide 100% recovery ratio, down to micron size, with no loss of production.
DOVE RIVERMINER® are configured with security system and locking mechanism to prevent theft of production.
DOVE RIVERMINER® are designed for automatic and simultaneous classification, concentration and 100% recovery with no loss of gold, diamonds, gemstones, and other metals and minerals.
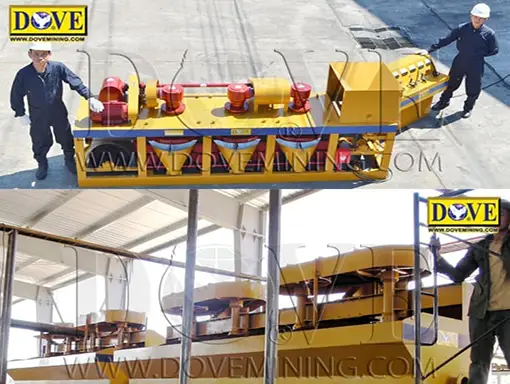
DOVE High Intensity Magnetic Separator / DOVE Flotation Circuit for Hard Rock Processing and Beneficiation
beneficiation plants
DOVE designs and manufactures high recovery Beneficiation Plants. Beneficiation plants are composed of different types of machines and separators depending on the metals and minerals composition and characteristics, designed for high economic recovery in a customized configuration that will meet the project’s specifications. These plants can include Flotation Machines, Dryers, High Intensity Magnetic Separators, High Tension Separators, etc. They can be used for both hard rock (primary) and alluvial (secondary) deposits.
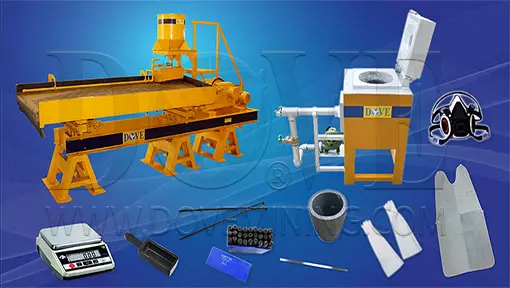
Gold Room Equipment
gold room
Every mining operation requires sophisticated gold room in order to ensure the highest recovery of gold production. To this end DOVE supplies and manufactures a complete range of equipment, instruments, tools and accessories, which includes Gold Concentrating Table, melting furnace, crucibles, ingot molds, scales, and assay instruments.
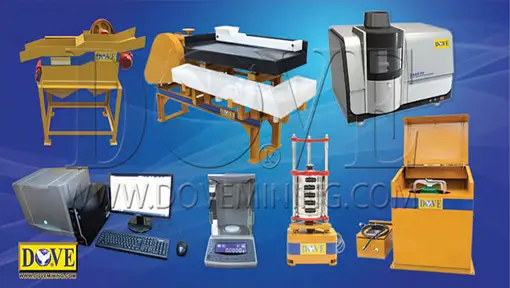
DOVE Laboratory Equipment
mineral assay laboratory instruments
DOVE supplies a full range of Laboratory Instruments, Equipment and accessories for minerals assay testing.
DOVE supplies Flame Atomic Absorption Spectrometer (AAS) for Fire Assay Analysis, Portable Mineral Analyzer and Professional Lab Mineral Analyzer for XRF Test, and equipment for Gravity Separation Test such as Lab Jig Concentrator and Lab Concentrating Tables. Several other types of equipment including Lab Induced Roll Lift Magnetic Separator, Lab Isodynamic Magnetic Separator, Lab High Tension Separator, Sampling Pulverizer, Sieve & Shakers, Bench Drill Machine and High Voltage Rectifier are part of the range of DOVE laboratory equipment.
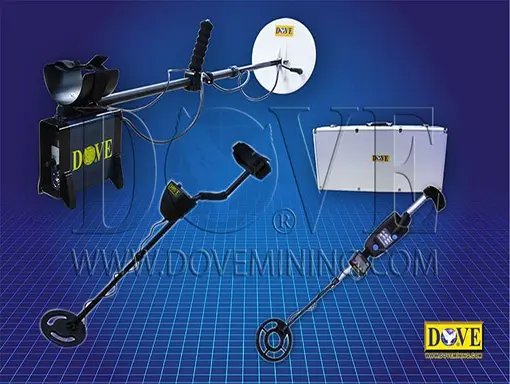
Metal Detectors
metal detectors
DOVE supplies advanced and highly accurate range of Metal Detectors. It is designed for ease of operation in highly mineralized soil condition. It provides a practical solution during exploration and prospecting different terrain with ease and dependability. DOVE Metal Detectors are designed for various depths and conditions.
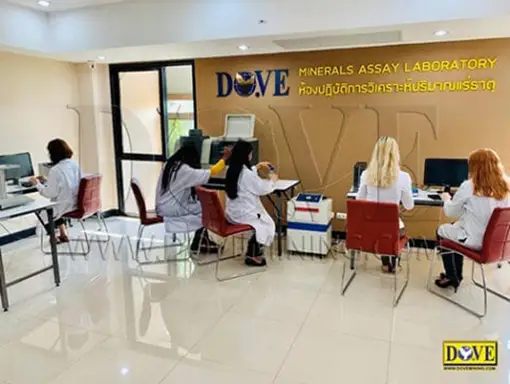
DOVE Mineral Laboratory Room
metals and minerals assay testing services
DOVE maintains the most sophisticated and advanced laboratory facilities in Asia to provide mineral assay services.
DOVE provides a complete range of minerals assay testing services, for both alluvial (placer) and hard rock (primary) deposits. DOVE mineral assay services include Gravity Separation, Fire Assay Analysis and XRF Analysis for identification of gold, platinum, other metals and minerals concentration and simultaneously analyze up to 32 other elements, metals and minerals.
“Reliable assay and minerals testing of your mine samples can lead you to the most efficient and best equipment configuration and plant design for the highest recovery of production and return of investment”.
CONTACT US BY E-MAIL
CONTACT DOVE EQUIPMENT AND MACHINERY
BY WHATSAPP (+66)-65-472-4266